Will OT take over MES?
October 2020
IT in Manufacturing
I don’t know. I’m in MES so I’m biased. No it will not. But if I were to look at it from a current reality and trend analysis, even a requirements analysis, I’d say maybe.
I don’t know. I’m in MES so I’m biased. No it will not. But if I were to look at it from a current reality and trend analysis, even a requirements analysis, I’d say maybe.
What is MES? Manufacturing Execution Systems (MES) in South Africa are based on computerised platforms that assist the manufacturing of products. The work in progress on equipment and machinery on the factory production floor is thus constantly monitored and information is recorded for analysis and evaluation.(Stolen from www.age.co.za).
What is OT? Operational Technology (OT) is a category of computing and communication systems designed to manage, monitor and control industrial operations, with a focus on the physical devices and processes they use. OT monitors and manages industrial process assets and manufacturing/industrial equipment. (Stolen from www.i-scoop.eu).
When I need to build relationships with plant guys, I do not differentiate MES from traditional IT, since traditional IT is what all of them know – computers and things. My go-to explanation is always, “It’s IT, just for your plant, designed and supported to your needs.” Traditionally MES features on the plant organogram just above the scada layer. The plant network is the de facto layer of IT that fetches plant data and streams it to the various MES systems, to feed and visualise the information to the enterprise levels above. In this depiction there is no MES. It’s IT and then it’s OT – interesting.
One can probably argue that OT might include MES, or it can operate simultaneously alongside the MES systems. I can subscribe to that definition, but at the same time, I feel it’s a waste of space and an unnecessary increase in complexity.
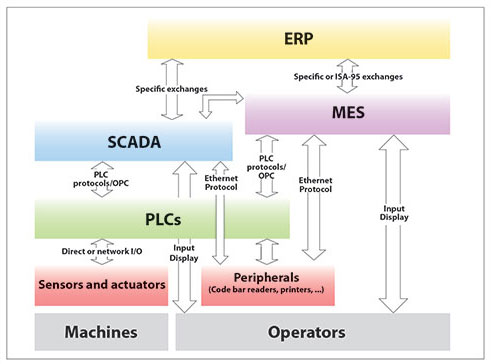
Scada vs MES integration with plant floor data – OT added.
IT/OT convergence
MES has been at the helm of steering manufacturing data to the business for decades. OT is an advancement of MES, so, unless we box MES as specifically designed for certain manufacturing processes and outcomes, I see no future for dedicated MES teams or systems, unless those teams and systems adopt the methodologies of converging IT and OT on the plant floor. I have yet to see a company that has three different technology departments: IT, MES and OT.
Data is an important commodity in any manufacturing company since it opens up insights they never thought they had. Data drives value, and evolves from the bottom up into meaningful information. Just so, I think MES needs to evolve into OT. MES leaders can leverage the foundation they have already established, and bring the manufacturing plant closer to the IT offerings of corporate. Or should MES serve as the bridge from OT to IT?
In this article, I do not address the skills required, the differences in protocols, the differences in networked security requirements, or the types of technology, I merely throw an idea out there to the IT in manufacturing community. An idea that I think could either solve the convergence of IT and OT or force the evolution of MES to OT, or increase the scope of MES to include OT technology. Whichever it is, the requirement for a convergence of technologies for the value of manufacturing plants is increasing, and companies are not necessarily concerned about what we in the MES industry call it. They simply want solutions that will help them dive deeper into specialised systems they need to keep up with the demands Industry 4.0 is throwing at them.
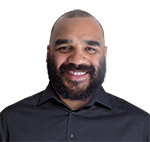
Lance Turner
Lance Turner is an MES specialist employed at Sasol’s Secunda plant. He has an honours degree in Information Systems with a focus on Enterprise Architecture design and solutions. A certified MESA MES/MOM student, his passion is amalgamating general IT across the manufacturing spectrum. Lance’s vision is for a converged IT and manufacturing discipline that will become the reality of Industry 4.0. His team motto is MES services that are always available, always stable, and always dependable.
For more information contact Lance Turner, Sasol, +27 17 610 6947, [email protected], www.sasol.com
Further reading:
Buildings in Africa’s urban evolution
Schneider Electric South Africa
IT in Manufacturing
Africa is now an urban continent. How does the continent mobilise to accommodate urban dwellers and maintain and implement critical infrastructure that allows for this expansion? Building management systems provide a tangible solution to optimise resource use, lower operations costs and ultimately contribute to a growing continent that also employs green practices.
Read more...
Black Rock Mining centralises mining operations with AVEVA
IT in Manufacturing
Black Rock Mine Operations replaced and upgraded its existing infrastructure, and installed additional capacity to expand production from 3 to 4,6 million tons in three years. The new system is powered by a suite of AVEVA solutions.
Read more...
The strategic role of technology in today’s economy
IT in Manufacturing
In an era of economic uncertainty and persistent market volatility, businesses are under immense pressure to manage costs while maintaining operational effectiveness. The role of chief information officers and chief technology officers has never been more critical, as they are tasked with leveraging technology not just as a tool for efficiency but as a strategic asset in navigating these turbulent times.
Read more...
Minutes to meltdown: surviving a cyber attack
IT in Manufacturing
Commvault recently hosted its Minutes to Meltdown event. Led by the company’s security experts, this was an interactive and detailed ransomware attack simulation designed to help companies understand how to respond in the event of a cyber attack.
Read more...
Siemens elevates automotive and aerospace simulation
Siemens South Africa
IT in Manufacturing
Siemens Digital Industries Software has announced the latest update to its Simcenter portfolio, delivering advancements in aerostructure analysis, electric motor design, gear optimisation and smart virtual sensing. These enhancements are designed to streamline workflows, accelerate certification and provide deeper insights into system performance.
Read more...
Automation in 2025: Navigating manufacturing innovation without the risk
IT in Manufacturing
During 2025, a wave of innovative technologies is expected to disrupt and change the way IT is applied to automation systems. The challenge lies in balancing the reliability of proven techniques with the potential of new technologies, all while minimising and controlling risk. This article explores ways to approach the latest information technologies effectively in a manufacturing context.
Read more...
South Africa’s AI revolution is here – but are we secure?
IT in Manufacturing
South African businesses are sprinting to embrace generative AI, lured by its potential to drive efficiency, productivity and innovation. But here’s the stark reality: without a rock-solid cybersecurity foundation, AI will become a Trojan horse, opening the floodgates to sophisticated cyber threats.
Read more...
Shaping data resilience strategies with AI and hybrid cloud solutions
IT in Manufacturing
In today’s rapidly evolving digital landscape, organisations are under growing pressure to secure their operations against increasingly sophisticated cyberthreats, including those that leverage AI to enhance the success rate of attacks. In this landscape, it has become essential to ‘fight fire with fire’ – harnessing AI as a means to counter these threats.
Read more...
Cloud or on-prem? Decoding the choices for South African enterprises
IT in Manufacturing
The debate between on-premise and cloud computing architectures remains a prominent topic among businesses, particularly in South Africa.
Read more...
Advancements in wire rope testing
IT in Manufacturing
Being able to get instant, real-time and portable detection of wire rope flaws can make a significant difference for operational teams. There have been a number of significant technological advancements and tools entering the market that help wire rope operators detect and resolve problems faster.
Read more...